Here is a small selection of Long River Machines in Action, where you can see various machines that are used in a Corrugating board manufacturing production line.
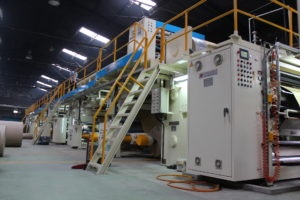
This project is running successfully and has reached remarkably important levels of production quantities.
A lot depends on the amount of time allocated to effectively training the operators on these modern high-speed Corrugators from Long River Machines.
So to achieve maximum productivity from the whole production line as efficiently as possible.
This process really starts at the very beginning of the project’s initiation. Now is the time to adopt a strategic pragmatic approach to the complete project, while taking everybody that’s going to be involved on board at an early stage.
Good Planning
Good planning pays dividends, and the sooner you get the operators on board the project the better. This means the sooner they will be able to reach their companies production goals in as short a period as possible.
As the machinery is installed and got ready for production runs. Many of the operators should be encouraged to make themselves familiar with all aspects of the capabilities of their new machines as soon as they can.
Then when test runs commence all operators need to be involved and observe, the progress of the test runs by the engineers. At this stage operators should be able to observe & determine what solutions are required to correct the faults or mishaps as they occur!
When the testing engineers have completed their work, truly little is required from them during the final production test runs. It is at this stage that operators and production personal and management start to move onto the live production runs.
This stage of events can be exciting for everyone involved with the project. It is exhilarating to see the production personal and the various machine operators start to take control of their new machinery, as they start to ramp up speed.
If they previously run their old machinery at say 130 mpm, then to see the delight on their faces as the speeds go up to say 200, 250, 300 mpm. At this point, they still have the machinery manufacturers’ support people standing close by. So, operators can feel confident that they are safe. If any mishaps should develop during their initial stages of controlling their new machinery, it’s easy to rectify.
Good Communications
To hear the headset communication and the chatter going on between the operators, you can now tell that these guys have got to grips with their new machinery, and within days they are now running production at higher levels than they could ever achieve with their old machinery.
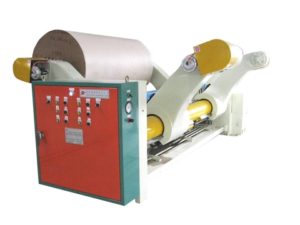
In some instants, this is not possible for example when a new range of machinery is introduced to the workforce that is not familiar with the new machinery or the process.
So ample time will be required for the new operators to see and feel their way around the new machines as they are being installed.
This may need a few organised visits when the installation people have finished for the day, or they have moved along to another part of the Corrugator installation work.
As the new Corrugator starts up production while various machinery engineers and production personal are to hand, machine operators are always enthusiastic to make a good start to take control of their new production line.
Efficient Running Long River Machines
It is now that your earlier instruction & training sessions will start to show, & how fast some people can-pick-up the necessary knowledge, which is required to operate their new machinery efficiently.

One of the best ways to offer this on-the-job expertise is to provide all personal with their own individual operating manuals, which are well documented and illustrated.
This helps to explain with ease, the methods of operating and controlling in detail, all the machines in the new production line.
Long River Machines the Mill Roll Stand & Auto Splicer
This photo shows the 2 previous images of two separate machines mounted together as one unit.
This is normally how these machines fit together and work as one unit to feed a continuous supply of paper into the corrugator.
This combination carries two reels of paper, one reel running and one reel ready to splice up as required. This feeds one continuous supply of paper that makes up one of the webs or plies that ends up in the corrugated board sandwich.
Depending on how many plies that a Corrugating machine may use, this determines how many of these Mill Roll Stands & Auto Splicer combinations that are in the production line. On a 5-ply corrugator, you will have 5 of these sets in the production line, for example.
Auto Paper Alignment
One of these auto paper alignment combination units is set up as the master ply. All the other plies follow the same edge alignment as this ply. Normally this web runs down the centre line of the corrugator.
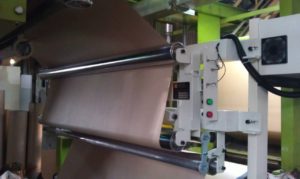
We use an automatic machine to maintain the web in the centre position as a first stage of the process.
This machine is called an automatic alignment unit. It is positioned just after the splicer and before the web pre-heater. This unit would be used on the master web to align it in the centre of the corrugator!
Then all other web alignment units would track this master web position so that all the various web liners or fluting materials are aligned when they enter the glue units and the single facers.
When the corrugated board sandwich enters the Double Backer or (heat chest) all the webs are closely aligned to the same centre line as the corrugated board travels through the various machines of the process.
While the auto-alignment units do their job, this means that the maximum amount of material is utilised for the finished order. This is achieved as the corrugated board will run through the slitter as intended. With the minimum continuous waste material being trimmed off, the running web on some corrugators can reach speeds of up to 450 mpm.
Break Outs
At these speeds nobody wants a “break out” or “jam-ups” because of poorly aligned web plies. In these situations, the rotary shear is activated, or “fired” and the running web is then diverted into the waste pit for several seconds.
As the old running web tail clears the slitter unit in that brief time, then the rotary shear is Fired again and the new web can be run through a second slitting unit and on through the NC Cutter, aka the (Knife Unit).
In a high percentage off breakouts that occur, they only last for a few seconds, and production continues at whatever speed the corrugator was previously running at. With no loss in production speed as on most modern corrugators, anybody on the take-off, may not even notice that a breakout occurred!
How are corrugated boxes made?
.
‘